About Us
About National HRD Network
The National HRD Network, established in 1986, is the National apex body of professionals committed to promoting the HRD movement in the country and enhancing the capability of human resource professionals through education, training, research and experience sharing. Established over 30 years ago, NHRDN is an autonomous, not-for-profit professionally managed organization, playing a catalyst role in grooming leaders for tomorrow. It has more than 12,000 members representing multinationals, public & private organizations including Government, MSME & NGOs spread across 30 chapters in India and serves as a reference point for HR Professionals in Indian Industry.
Our Value Proposition
National HRD Network through its various initiatives provides the following value propositions to its members and the larger HR community:
- Enhancing Capabilities: One of the key objectives of NHRDN is to build capacity among HR professionals. Through various initiatives, NHRDN strives to build individual and organizational capabilities.
- Pride of Association: NHRDN provides a national and international linkages to HR professionals across the country and industry on a common platform.
- Thought Leadership: NHRDN provides knowledge and insights from eminent thought leaders.
- Networking: NHRDN provides the opportunity to meet and interact with people across industry facilitating growth in terms of knowledge, sharing practices and recognition.
Current Leadership Team
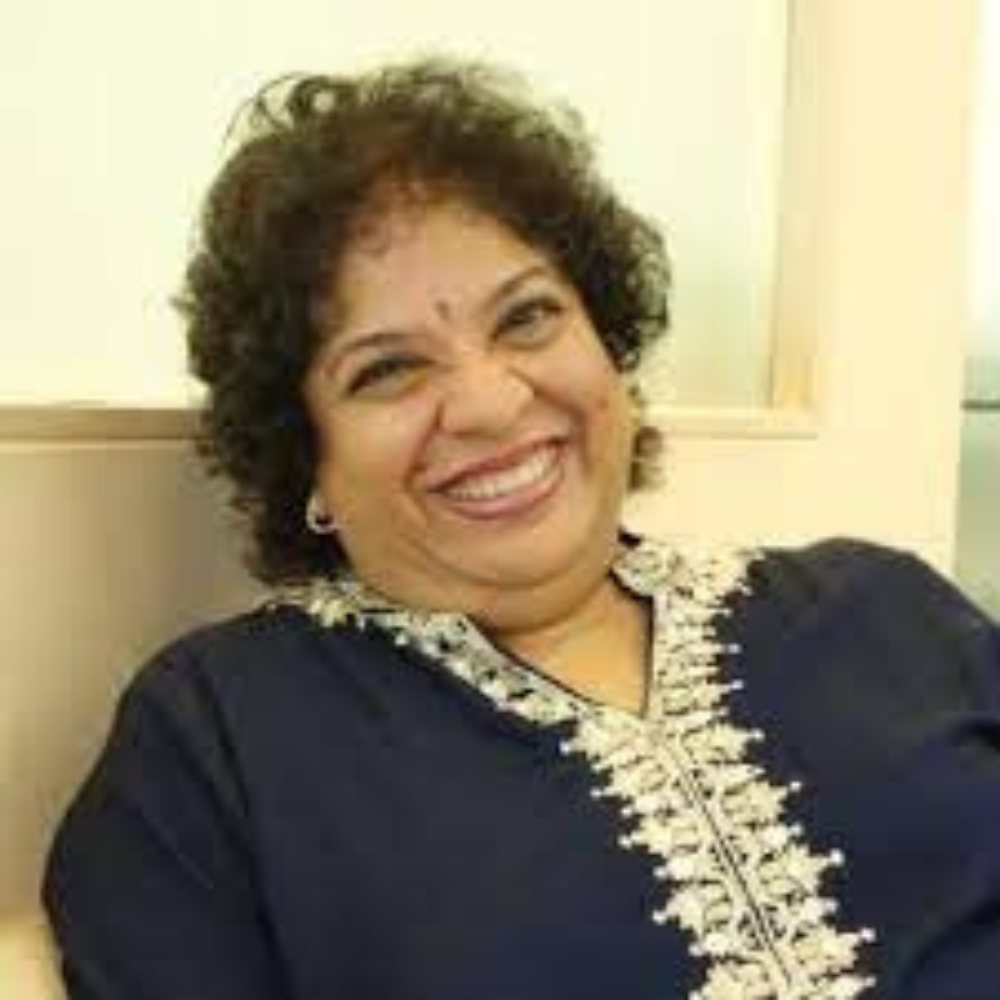
Mona Cheriyan
Thomas Cook (India) Ltd
President & Group Head HR
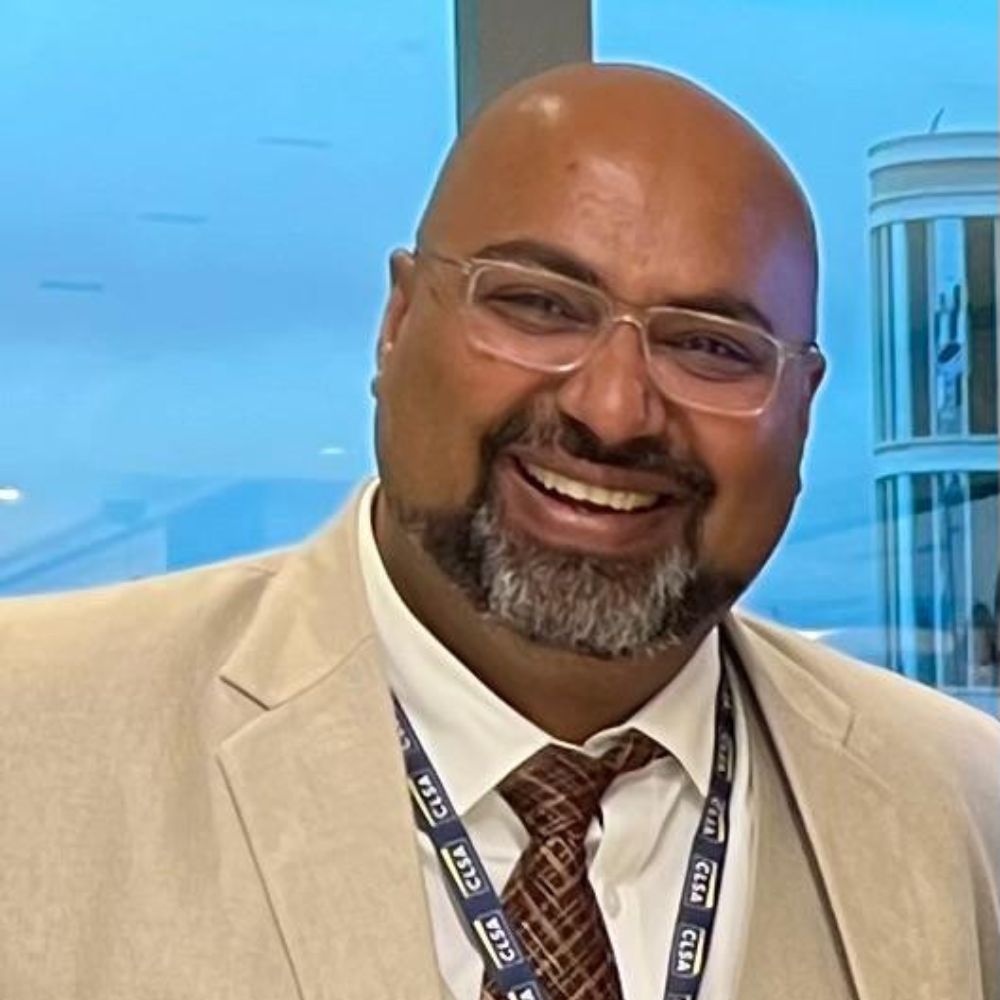
Ashutosh Srivastava
CITICS CLSA
Head of India HR
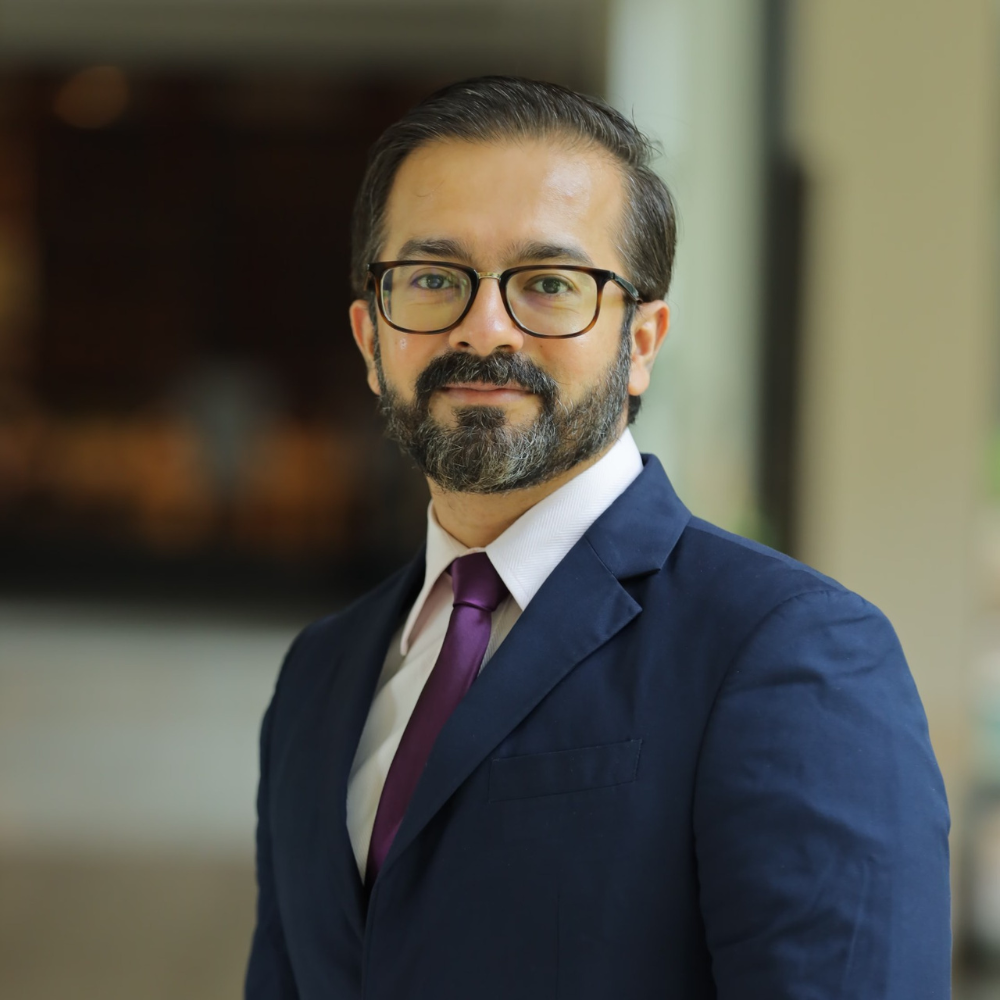
Prakhar Tripathi
Deloitte
Partner
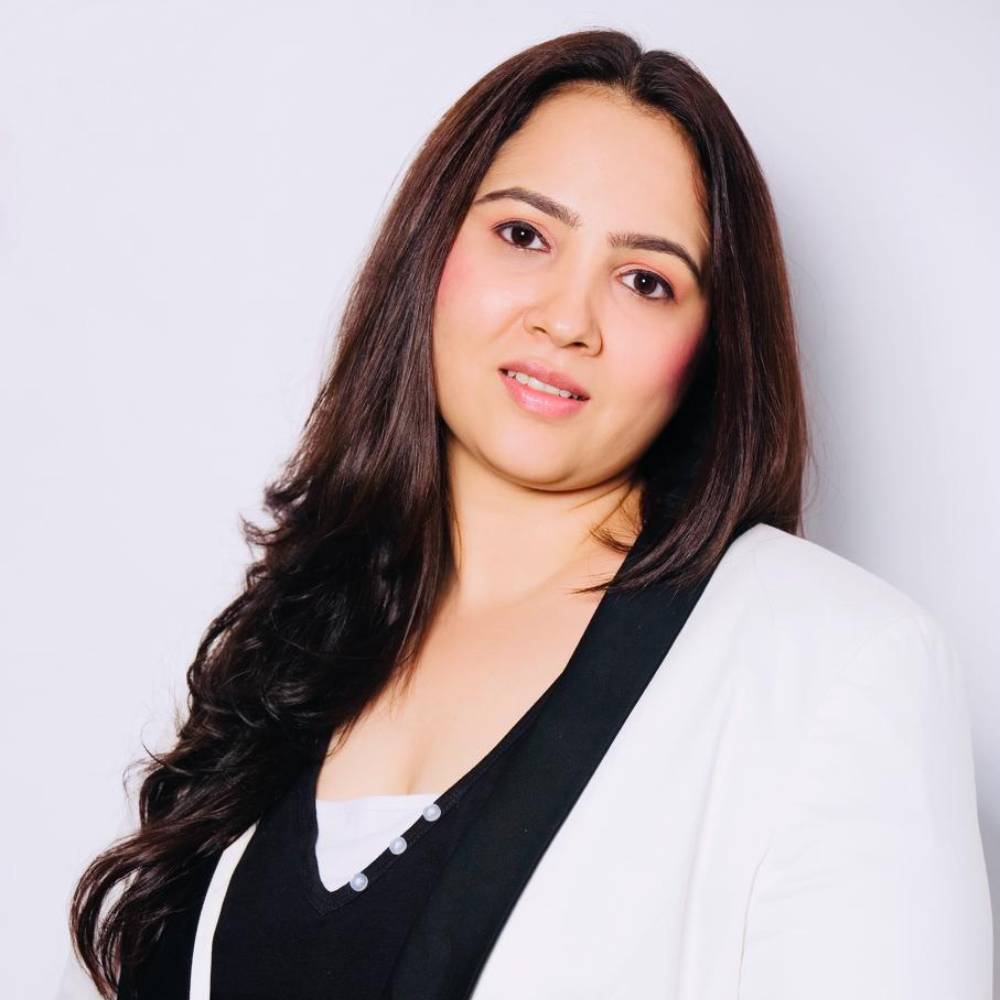
Shweta Pathak
Cornerstone OnDemand
Marketing Leader, India
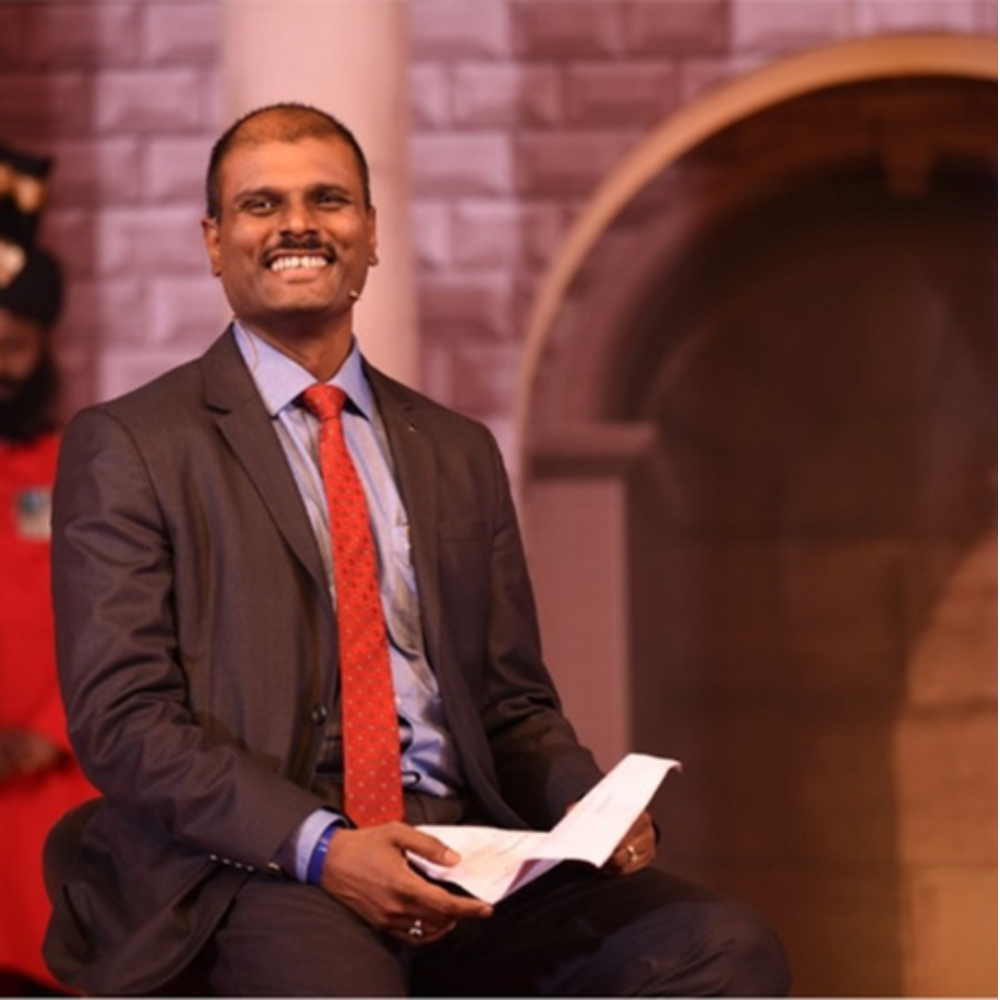
Amitabh Kumar Singh
ICICI Bank
Head Business HR
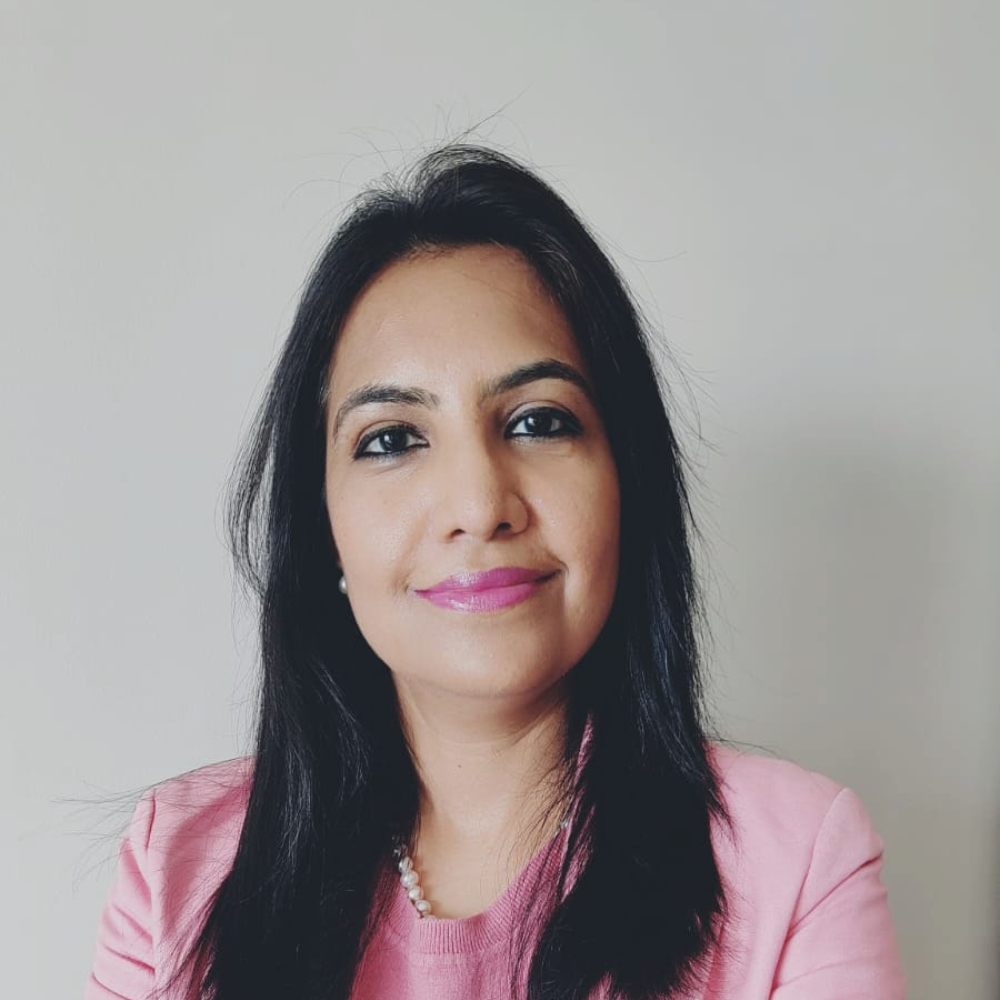
Tanisha Saraf
Aditya Birla Group - UltraTech Cement
Head Talent Staffing & Employer Branding
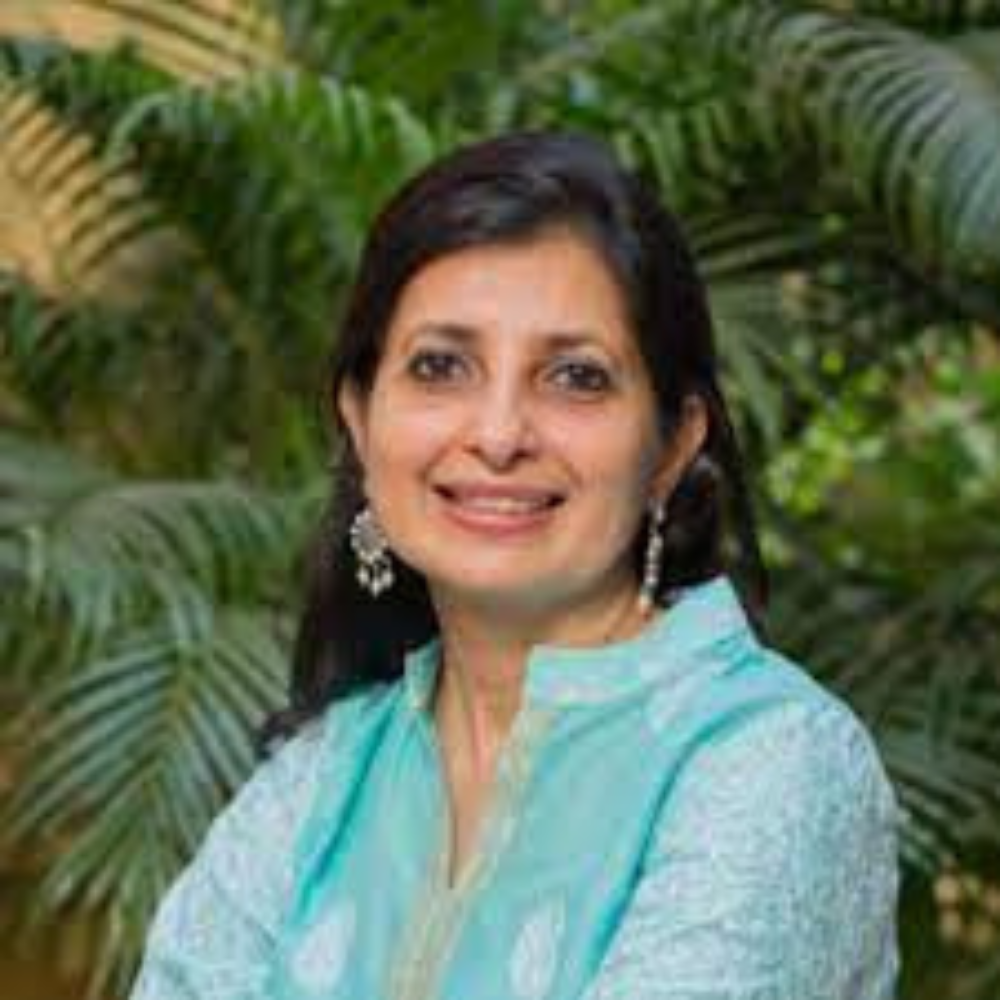
Dr. Snehal Shah
SP Jain Institute of Management & Research
Associate Dean, Academics & Research Professor - Organisation & Leadership Studies
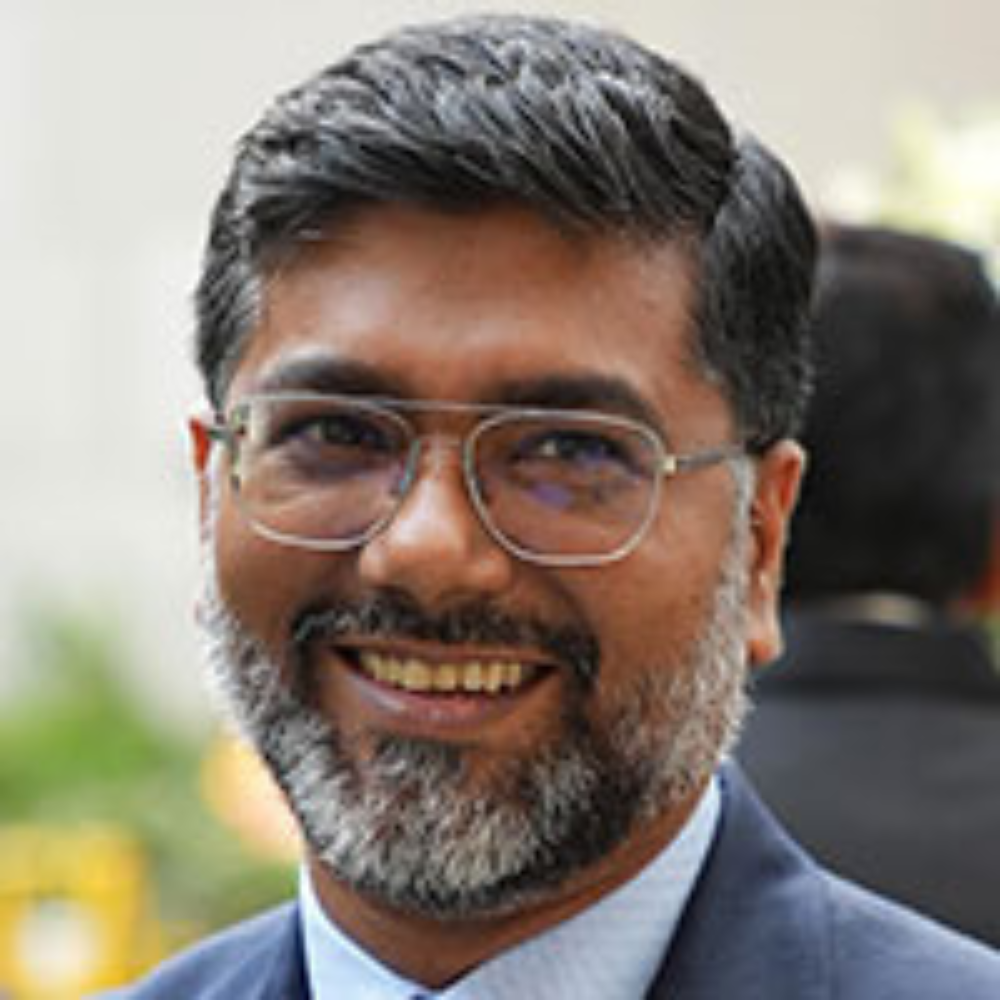
Tathagata Basu
Piramal Pharma Limited
Chief Talent Officer
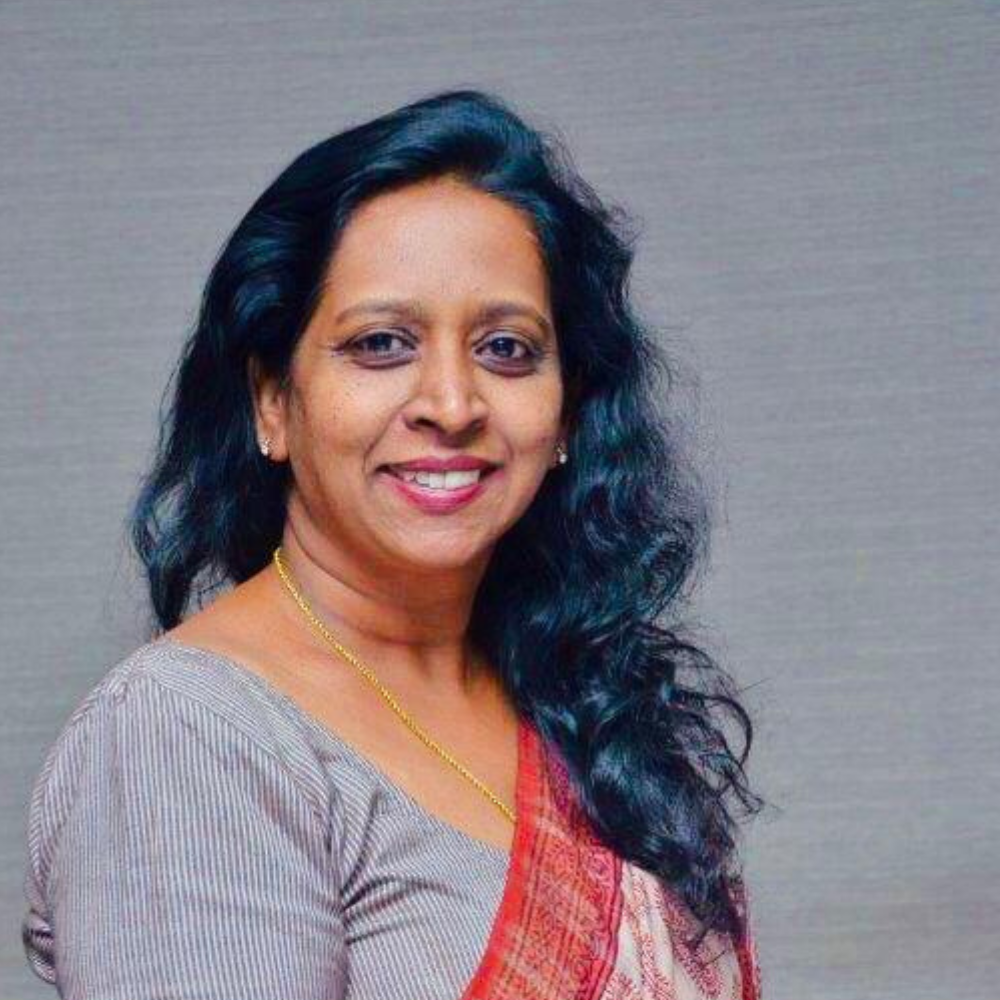
Zenith Nayar
L&T Technology Services Ltd
Head – HR Transformation
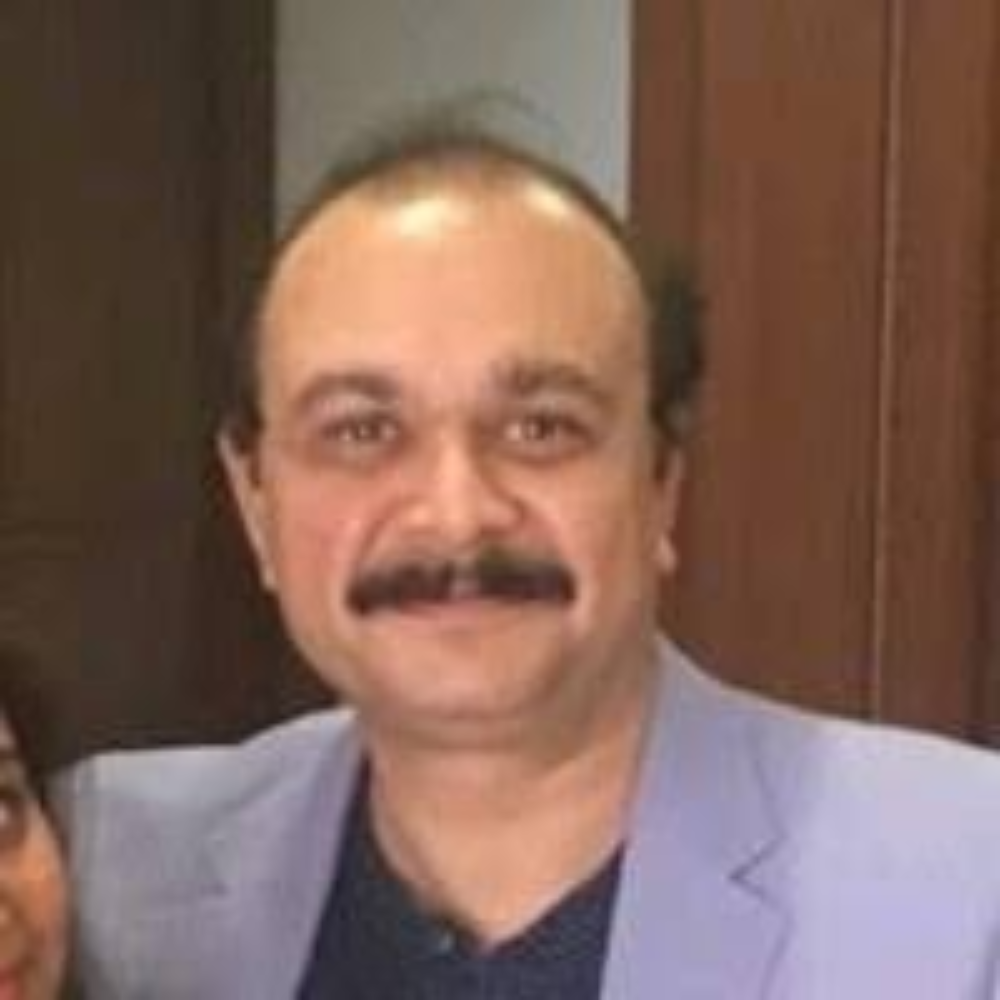
Aniruddha Khekale
Waaree Group
Chief Human Resources Officer
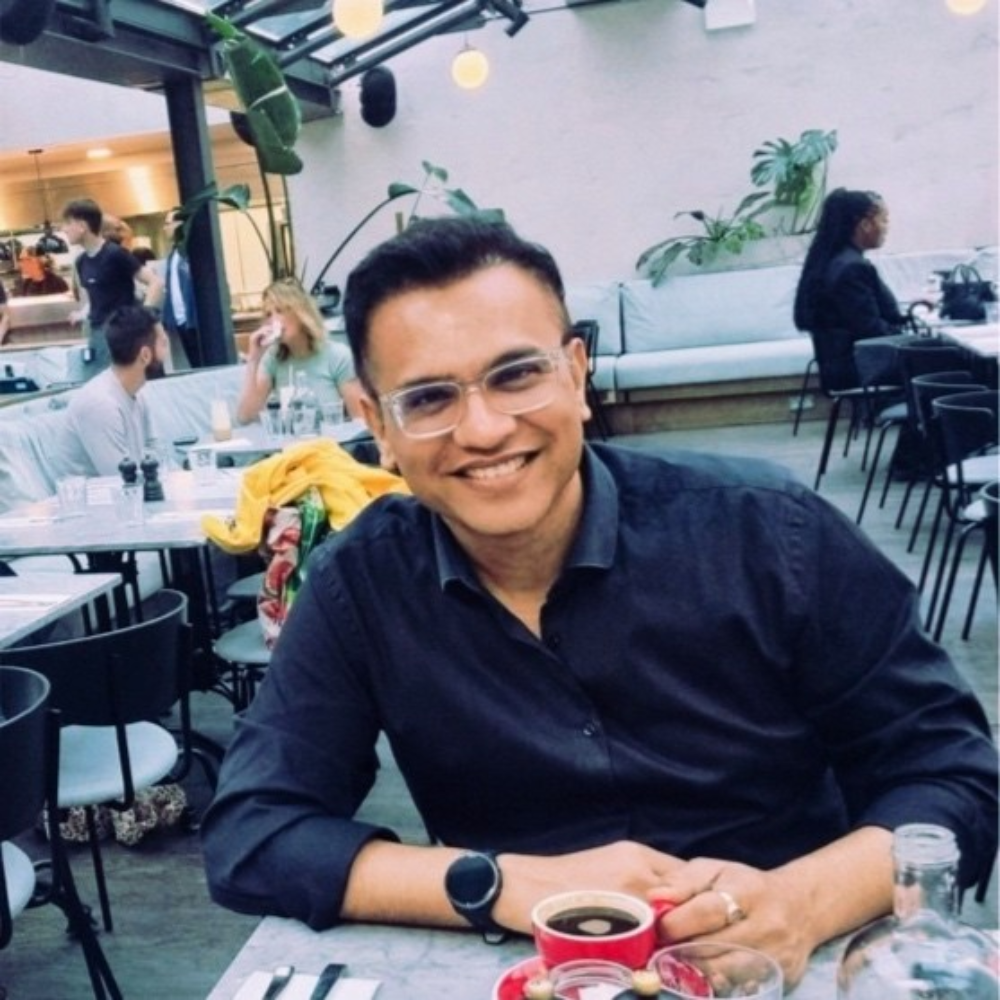
Rahul Pinjarkar
Tata Chemicals
Chief Human Resource Officer
Past Mumbai Chapter Presidents
- 1985 – 1987 : T. P. Raman
- 1987 – 1989 : Ginil Shirodkar, Director – Strides International
- 1989 – 1991 : C. M. Srivastava, Independent Consultant
- 1991 – 1993 : C.M. Srivastava/Leslie Rebello
- 1993 – 1995 : Leslie Rebello, Director – L. R. Associates Pvt. Ltd.
- 1995 – 1997 : Dr. P. V. Bhide, President – Corp. HR, J. K. Industries Ltd.
- 1997 – 2001 : George Kunnath, Independent Consultant
- 2001 – 2004 : S. S. Muzumdar, Director HR ( Retd.), Siemens Ltd.
- 2004 – 2007 : Vineet Kaul, Chief People Officer, Hindalco Industries Ltd.
- 2007 – 2010 : Rajeev Dubey, President (HR, After Market & Corp.Service ), Mahindra & Mahindra Ltd
- 2010 – 2012 : Prof. Dr. Uday Salunkhe, Group Director, We School
- 2012 – 2015 : Yogi Sriram, Sr. Vice President – Corp. HR., Larsen & Toubro Ltd.
- 2015 – 2017 : Judhajit Das, Chief Human Resources, ICICI Prudential Life Insurance Com. Ltd.
- 2017-2019 : M.T. Laxmanan, Head Talent Management & Total Rewards, Larson & Toubro Ltd.
- 2019-2021: Vikram Tandon – Head of Human Resources-HSBC India
- 2021-2023: Prof. Vijayan, President & Dean-HR & Industry- Academia Interface , Chief Human Resources Officer & Head- Career Management Centre, Welingkar Institute of Management